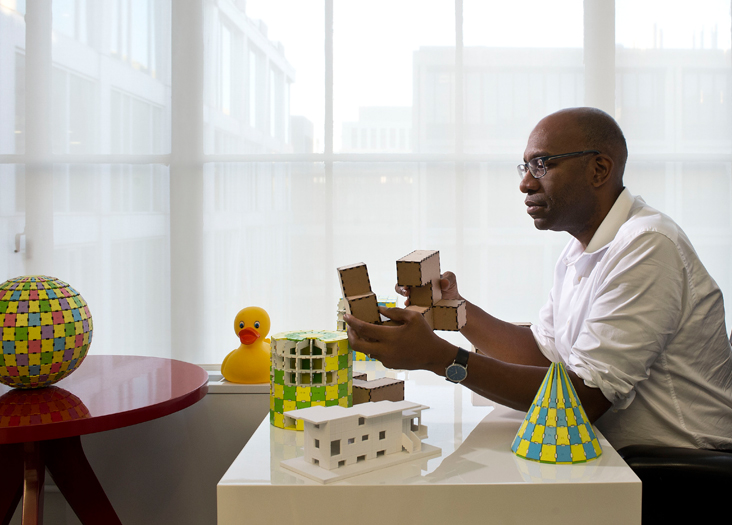
Larry Sass: A vision for new buildings to rise faster, use fewer resources, and cost less, thanks to digital fabrication.
PHOTO ILLUSTRATION: LEN RUBENSTEIN
This transformation will be made possible through digital fabrication, a new delivery system for buildings that will enable architects to send computer-designed plans directly to manufacturing—perhaps soon to be 3-D printed.
“There’s a lot of research on the design and organization of cities and how cities should develop over time. But there is almost no research on how to manufacture and make the buildings you design,” says Sass, who does exactly such research as an associate professor of architecture and director of MIT’s Digital Design Fabrication Group.
Building construction essentially hasn’t changed since the 1800s; it remains slow, labor-intensive, and costly. Digital fabrication offers a streamlined process in which a computer-designed building can be manufactured as a sequence of precision-cut, interlocking parts that can be pieced together on site like a giant jigsaw puzzle, saving on parts and labor.
“It’s the right delivery system for the developing world, because the developing world doesn’t have an infrastructure of tools, air guns, saws, and power,” Sass says. Start-up costs are also low since computer numerical control (CNC) machines are inexpensive and portable. “Design and high-quality construction is mostly for the rich,” says Sass, who was raised in Harlem. “I’ve always wanted to figure out how to bring design choice and architectural delight to the poor.”
Digital fabrication relies on three technologies developed at MIT: CNC, invented in the 1950s to enable computers to control machines; computer-aided design software, created in the 1960s for drawing structures; and 3-D printing, a process that emerged in the 1980s for making solid models from digital designs. Combining these techniques enables designs to be tested accurately through rapid prototyping; the computer-drawn plans are so precise that any building that functions in prototype is guaranteed to scale up successfully.
“The Industrial Age was all about making identical copies of one design. The Information Age is about the simple manufacturing of infinite design possibilities through the application of a finite set of rules for manufacturing,” Sass says. “The challenge is figuring how to write new software that allows you to decompose very large designs into thousands of small parts for manufacturing.”
As a proof of concept, Sass built a digitally fabricated house for an exhibit at the Museum of Modern Art in New York in 2008. Prototyped at MIT at 1/6 scale, the full-size “printed house” was a complete success, taking just days to hammer together all 5,200 pieces.
Now Sass is developing ways to digitally reproduce objects directly from photographs in the hopes of speeding up the reconstruction needed after storms and other disasters. “You take photos of a house, run them through some software, and the machine makes all the components of the house that was just lost,” he says. “Imagine. Using photos and large-scale 3-D printing, you could reconstruct someone’s house in about six days.”